Методика модернизации сварочных технологий: от теории к практике
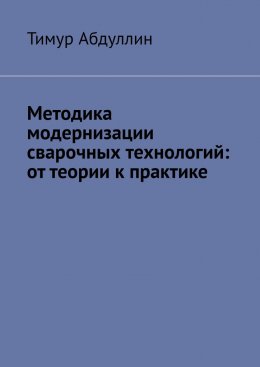
© Тимур Зуфарович Абдуллин, 2025
ISBN 978-5-0065-2622-8
Создано в интеллектуальной издательской системе Ridero
О монографии
Монография представляет собой исследование современных методов оптимизации сварочных процессов, акцентируя внимание на теплоустойчивых сталях. Автор, подчёркивает важность разработки эффективных технологий, что делает его работу особенно ценной для специалистов в этой области.
Эта монография станет надёжным источником для профессионалов, работающих в области машиностроения и технологий сварки.
Введение
Экономическое развитие страны напрямую зависит от рационального использования материальных, энергетических и трудовых ресурсов. Одним из перспективных направлений в этой области является повышение эффективности сборки заготовок и конструктивных элементов машин и агрегатов, а также создание менее энергоёмких технологических процессов, основанных на широком применении различных методов обработки металлов.
В нефтеперерабатывающей промышленности существует значительная потребность в оборудовании, изготавливаемом из теплоустойчивых сталей, таких как 12МХ. Эти стали предназначены для длительной эксплуатации при температурах до 550—570ºС и находят широкое применение в машиностроении для производства труб паронагревателей, трубопроводов и коллекторных установок высокого давления, а также для поковок паровых котлов и паронагревателей.
Также имеется необходимость в использовании теплоустойчивых сталей типа 12МХ для изготовления крупногабаритных сварных сосудов и аппаратов в нефтегазохимическом аппаратостроении. Эти стали обладают высокими прочностными и антикоррозионными свойствами при высоких температурах, особенно при наличии бейнитной или сорбитной структуры с равномерно распределенными мелкодисперсными карбидами.
Однако в легированных сталях типа 12МХ (включая 15ХМ и 12Х1МФ), содержащих стойкие карбидосодержащие элементы, такие как молибден, хром и ванадий, при огневой резке и сварке могут возникать участки с закалочными структурами. Это происходит на околошовных участках зоны термического влияния (ЗТВ), где температура превышает Ас3, а также на участках, подвергнутых нагреву до температуры Ас1, что приводит к снижению прочностных свойств.
Процесс изготовления оборудования из теплоустойчивых сталей типа 12МХ с применением сварки требует предварительного подогрева до температуры 150—200ºС и незамедлительной термической обработки при температуре 670—690ºС для снятия остаточных сварочных напряжений и предотвращения образования холодных трещин. Однако такая термическая обработка является сложным и энергоёмким процессом, который трудно осуществить в полевых условиях.
Исследование возможности снятия остаточных напряжений в конструкциях аппаратов с помощью циклического нагружения (вибрационной обработки) представляет собой актуальную задачу. Важно найти способы управления характером и уровнем остаточных напряжений, что позволит повысить технологическую прочность и качество аппаратов нефтеперерабатывающей промышленности. На основе работ таких учёных, как В. М. Сагалевич, А. М. Ким-Хенкин, К. М. Рагульскис, О. Г. Чикалиди, А. М. Велбель и других, выдвинуто предположение о возможности изменения характера и снижения уровня остаточных сварочных напряжений в различных конструкциях с помощью пластического деформирования или вибрационной обработки. Проведённые исследования подтвердили возможность управления остаточными напряжениями в металлических конструкциях и в ряде случаев замены дорогостоящей термической обработки на вибрационную.
Предварительный подогрев свариваемых конструкций снижает производительность и является сложным энергоёмким процессом. Небольшие отклонения от нормируемой технологии подогрева и режимов сварки могут привести к снижению прочности сварного соединения. В то же время, вибрационная обработка свариваемых элементов, проводимая в процессе сварки, является альтернативным методом снижения остаточных напряжений и повышения прочности сварных соединений.
В данной задачей совершенствования технологического процесса изготовления нефтегазохимического оборудования с использованием менее энергоёмких методов, в частности, применения вибрационной обработки в процессе сварки. Для достижения этой цели необходимо провести комплекс теоретических и экспериментальных исследований, которые включают следующие задачи:
• Установить характер распределения остаточных напряжений и деформаций, возникающих в процессе вибрационной обработки сварного соединения из стали 12МХ, для оценки её влияния на эффективность процесса.
• Оценить влияние вибрационного воздействия в процессе сварки на технологическую прочность и механические свойства сварного соединения из стали 12МХ.
• Разработать практические рекомендации для совершенствования технологии изготовления сварного нефтеперерабатывающего оборудования оболочкового типа из теплоустойчивых сталей типа 12МХ с использованием вибрационной обработки свариваемых деталей в процессе сварки.
Автор выражает благодарность заведующему кафедрой, профессору и научному руководителю И. Г. Ибрагимову за поддержку в проведении исследований, а также к. т. н. А.М. Файрушину за постоянную помощь в работе.
Глава 1. Анализ технологии изготовления сварного оборудования из стали 12МХ
1.1. Применение стали 12МХ в нефтегазовом оборудовании
Теплоустойчивыми называют стали, предназначенные для длительной эксплуатации при температурах до 600° C. Эти стали находят широкое применение в энергетических и нефтехимических установках. В условиях длительной работы под напряжением при высоких температурах теплоустойчивые стали должны обладать высокой стойкостью к ползучести, длительной прочностью, стабильностью свойств во времени и жаростойкостью. Достижение перечисленных свойств при экономичном легировании возможно благодаря использованию хромомолибденовых и хромомолибденованадиевых сталей перлитного класса.
Хромомолибденовые стали, такие как 12МХ, 15ХМ, 20ХМЛ и 15Х5М, с ферритно-перлитной структурой, применяются для работы при температурах 500—550° C. Хромомолибденованадиевые стали, например, 12Х1МФ, 15Х1М1Ф, 20ХМФЛ, 15Х1М1ФЛ и 12Х2МФСР, предназначены для эксплуатации при температурах 550—580° C. Более высокие жаропрочные свойства хромомолибденованадиевых сталей обусловлены не только стабилизацией карбидной фазы ванадием, но и применением упрочняющей термической обработки, обеспечивающей образование бейнитной структуры.
Сварка теплоустойчивых сталей сопровождается изменением свойств свариваемого металла, связанным с расплавлением и кристаллизацией при образовании шва, а также структурными изменениями и упругопластическими деформациями в околошовной зоне. Это приводит к физико-химической неоднородности сварных соединений и образованию местного сложнонапряженного состояния, что может ухудшить работоспособность и снизить эксплуатационную надёжность конструкций.
Металлургическая свариваемость теплоустойчивых сталей, определяемая их поведением при плавлении, металлургической обработке и последующей кристаллизации шва, не вызывает значительных осложнений. Современные технологии сварки и сварочные материалы обеспечивают необходимую стойкость швов к образованию горячих трещин и высокие характеристики их работоспособности, соответствующие требованиям, предъявляемым к основному металлу. Однако тепловая свариваемость может осложняться охрупчиванием металла из-за образования метастабильных структур в околошовной зоне, нагретой выше температуры Ас3, и разупрочнением в участках, нагретых в интервале температур Ас3 – температура отпуска стали. Образование хрупких структур (троостита, мартенсита) и суммирование напряжений, вызванных неравномерным нагревом и структурными превращениями, могут привести к потере пластичности металла и вызвать разрушение конструкций в процессе их изготовления. Для предотвращения образования холодных трещин необходимо использовать сопутствующий нагрев во время сварки, а в некоторых случаях – выдержку сварных соединений при определённой температуре после окончания сварки.
Эксплуатационная надёжность конструкций из металла повышенной толщины может быть обеспечена после стабилизации структуры и снятия напряжений путём отпуска сварных соединений. При этом температура отпуска сварных соединений хромомолибденованадиевых сталей должна быть не ниже 700° C, поскольку выпадение дисперсных карбидов ванадия из твёрдого раствора при низких температурах отпуска может привести к охрупчиванию металла околошовной зоны и возникновению локальных разрушений сварных соединений как в процессе отпуска, так и в ходе эксплуатации конструкций.
Учитывая все положительные технологические и эксплуатационные свойства стали 12МХ, очевидна необходимость ее применения. Эта сталь может использоваться для изготовления труб пароперегревателей, трубопроводов и коллекторных установок высокого давления, поковок для паровых котлов и паропроводов, деталей цилиндров газовых турбин, а также в качестве основного слоя при производстве горячекатаных двухсловных коррозионностойких листов. Рекомендуемая температура применения стали 12МХ составляет до 510° C, температура интенсивного окалинообразования – 570° C, а срок службы – более 10 000 часов.
1.2. Химический состав и физические свойства стали 12МХ
Сталь 12МХ относится к группе теплоустойчивых низколегированных сталей перлитного класса, предназначенных для эксплуатации в условиях повышенных температур и давления. Данная сталь обладает оптимальным сочетанием механических свойств и термостойкости, что делает её подходящей для изготовления оборудования, используемого в нефтегазовой отрасли.
Химический состав стали 12МХ представлен в таблице 1.1.:
Таблица 1.1. Химический состав в % стали 12МХ
Механические свойства стали 12МХ при температуре 20° C приведены в таблице 1.2.:
Таблица 1.2. Механические свойства стали 12МХ
при t=20° C
Твёрдость материала после отжига не должна превышать 217 HB, что подтверждает его способность сохранять необходимые механические свойства после термической обработки.
Таким образом, сталь 12МХ, обладая сбалансированным химическим составом и соответствующими механическими свойствами, является оптимальным выбором для применения в нефтегазовом оборудовании, где требуется высокая прочность, термостойкость и надёжность в эксплуатации.
1.2.1. Технология сварки конструкций из стали 12МХ
Теплоустойчивость сварных соединений оценивают отношением длительной прочности металла соединения и основного металла – коэффициентом теплоустойчивости.
Теплоустойчивые стали должны обладать жаростойкостью, длительной прочностью, стабильностью свойств во времени и сопротивлением ползучести: их пластическая деформация при постоянной нагрузке с течением времени должна возрастать незначительно, чтобы работать при высоких температурах,. Все это достигается введением в состав сталей 0,5…2,0% хрома, 0,2…1,0% молибдена, 0,1 …0,3% ванадия и иногда небольших добавок редкоземельных элементов. Сочетание механических свойств изделий из теплоустойчивых сталей достигается термообработкой: нормализацией или закалкой с последующим высокотемпературным отпуском. Это обеспечивает мелкозернистую структуру, состоящую из дисперсной ферритокарбидной смеси.
Физическая свариваемость теплоустойчивых сталей, определяемая отношением металла к плавлению, металлургической обработке и к последующей кристаллизации шва не вызывает затруднений. Современные сварочные материалы и технология сварки обеспечивают требуемые свойства и стойкость металла шва против горячих трещин, но в тоже время сварные соединения обладают склонностью к холодным трещинам и к разупрочнению металла в зоне термического влияния (ЗТВ). Поэтому требуется использовать сопутствующий сварке местный или предварительный общий подогрев изделия. Это уменьшит разницу температур в зоне сварки и на периферийных участках, что снижает возникающие напряжения в металле. Уменьшается скорость охлаждения металла после сварки больше аустенита превращается в мартенсит при высокой температуре, когда металл пластичен. Напряжения, возникающие из-за разницы объемов этих фаз, будут меньше, при этом вероятность образования холодных трещин снизится. В свою очередь применяя подогрев, нужно учитывать, что излишне высокая температура приводит к образованию грубой ферритно-перлитной структуры, не обеспечивающей необходимую длительную прочность и ударную вязкость сварных соединений. С целью снизить опасность возникновения холодных трещин можно, произвести отпуск деталей, выдерживая их при температуре 150…200 °С сразу после сварки в течение нескольких часов. За это время завершится превращение остаточного аустенита в мартенсит и удалится из металла большая часть растворённого в нем водорода. Разупрочнение теплоустойчивых сталей в ЗТВ зависит также от параметров режима сварки. Повышение погонной энергии сварки увеличивает мягкую разупрочняющую прослойку в ЗТВ, которая может быть причиной разрушения жёстких сварных соединений при эксплуатации, особенно при изгибающих нагрузках. Основные способы сварки конструкций из теплоустойчивых сталей – это дуговая и контактная стыковая. Последнюю используют для сварки стыковых соединений труб нагревательных котлов в условиях завода изготовителя.
Дуговую сварку производят электродами с покрытием, в защитных газах и под флюсом. Подготовку кромок деталей при всех способах дуговой сварки производят механической обработкой. Допускается применение кислородной или плазменной резки с последующим удалением слоя повреждённого металла толщиной не менее 2 мм.
Дуговую сварку производят при температуре окружающего воздуха не ниже 0 °С с предварительным и сопутствующим сварке местным или общим подогревом. Температура подогрева зависит от марки стали и толщины свариваемых кромок. Хромомолибденовые стали при толщине кромок до 10 мм, а хромомолибденованадиевые – до 6 мм можно сваривать без подогрева. Сталь 12МХ, например, толщиной 10…30 мм надо подогревать до температуры 150…200 °С, а больше 30 мм – до температуры 200…250 °С. При многопроходной автоматической сварке под флюсом минимальную температуру подогрева можно снижать на 50 °С. Аргонодуговую сварку корневого шва стыков труб выполняют без подогрева.
После сварки производят местный отпуск сварных соединений или общий отпуск всей сварной конструкции. Хромомолибденовые стали нагревают при отпуске до температуры 670…700 °С с выдержкой при этой температуре от одного до трех часов в зависимости от толщины сваренных кромок, хромомолибденованадиевые – до температуры 740…760 °С с выдержкой от двух до десяти часов. Чем больше в стали хрома, молибдена, ванадия, тем больше должны быть температура и время отпуска. Отпуск стабилизирует структуру и механические свойства соединений, снижает остаточные напряжения, однако он не позволяет полностью выровнять структуру и устранить разупрочненную прослойку в зоне термического влияния. [124, 126. 127, 129].
Ручную дуговую сварку теплоустойчивых сталей ведут электродами из малоуглеродистой сварочной проволоки с основным (фтористо-кальциевым) покрытием, через которое вводят в шов легирующие элементы. Этот тип покрытия хорошо расчисляет металл шва, обеспечивает малое содержание в нем водорода и неметаллических включений, надёжно защищает от азота воздуха. Это позволяет получать высокую прочность и пластичность шва. Однако для электродов с таким покрытием характерна повышенная склонность к образованию пор при удлинении дуги, наличии ржавчины на поверхности свариваемых кромок и при небольшом увлажнении покрытия. Поэтому нужно сваривать предельно короткой дугой, тщательно очищать кромки и сушить электроды перед их применением при температуре 80… 100 °С. Хромомолибденовые стали сваривают электродами типа Э-09МХ (ГОСТ 9467—75) марки ЦУ-2ХМ диаметром 3 мм и более, а также ЦЛ-38 диаметром 2,5 мм, хромомолибденованадиевые – электродами типа Э-09Х1МФ марок ЦЛ-39 диаметром 2,5 мм, ЦЛ-20, ЦЛ-45 диаметром 3 мм и более. Сварку ведут на постоянном токе обратной полярности узкими валиками без поперечных колебаний электрода с тщательной заваркой кратера перед обрывом дуги. Когда подогрев свариваемых изделий и их термообработка после сварки невозможны или если необходимо сваривать перлитные теплоустойчивые стали с аустенитными, допускается использование электродов на никелевой основе марки ЦТ 36 или проволоки Св 08Н60Г8М7Т при аргонодуговой сварке.
Теплоустойчивые стали сваривают дуговой сваркой плавящимся электродом в углекислом газе и вольфрамовым электродом в аргоне. Сварку в С02 из-за опасности шлаковых включений между слоями используют обычно для однопроходных швов и для заварки дефектов литья. Сварку ведут на постоянном токе обратной полярности с присадочной проволокой (ГОСТ 2246—70) Св 08ХГСМА для хромомолибденовых сталей или Св 08ХГСМФА для хромомолибденованадиевых сталей. Для проволоки диаметром 1,6 мм сила сварочного тока 140…200 А при напряжении дуги 20…22 В, а диаметром 2 мм 280… 340 А при 26…28 В.
Ручная аргонодуговая сварка используется для выполнения корневого шва при многопроходной сварке стыков труб. Автоматической сваркой в аргоне сваривают неповоротные стыки паропроводов в условиях монтажа. При аргонодуговой сварке хромомолибденовых сталей.
Автоматическую дуговую сварку под флюсом используют на поворотных стыках трубопроводов, коллекторов котлов, корпусов аппаратов химической промышленности и других изделиях с толщиной стенки 20 мм и более. Применяют низкоактивные по кремнию и марганцу флюсы ФЦ-11, АН-22. Этим достигается стабильность содержания Si и Мп в многослойных швах и низкое содержание в них оксидных включений – продуктов процесса восстановления марганца. Сварку под флюсом ведут со скоростью 40…50 м/ч на постоянном токе обратной полярности силой 350…400 А при напряжении дуги 30…32 В. Высокая скорость сварки уменьшает погонную энергию, что снижает разупрочнение хромомолибденованадиевых сталей в околошовной зоне. Применяют проволоку диаметром 3 мм Св 08МХ и Св 08ХМ для хромомолибденовых сталей и Св 08ХМФА для хромомолибденованадиевых сталей. Можно применять проволоку диаметром 4 и 5 мм, увеличив соответственно силу тока до 520…600 А и 620…650 А при напряжении дуги 30…34 В. [135]
1.3. Причины образования холодных трещин
Холодные трещины объединяют категорию трещин в сварном соединении, формальными признаками которых являются: возможность их визуального наблюдения практически сразу после охлаждения соединения; их блестящий кристаллический излом без следов высокотемпературного окисления.
Холодные трещины – локальные хрупкие разрушения материала сварного соединения, возникающие под действием собственных сварочных напряжений. Размеры холодных трещин соизмеримы с размерами зон сварного соединения. Локальность разрушения объясняется частичным снятием напряжений при образовании трещин, а также ограниченностью зон сварного соединения, в которых возможно развитие трещин без дополнительного притока энергии от внешних нагрузок. [136]
Характерными особенностями большинства случаев образования холодных трещин являются следующие:
1) наличие инкубационного периода до момента образования очага трещин;
2) образование трещин происходит при значениях напряжений, составляющих менее 0,9 кратковременной прочности материалов в состоянии после сварки. Эти особенности позволяют отнести холодные трещины к замедленному разрушению свежезакаленной стали.
При сварке легированных сталей холодные трещины могут образовываться, если стали претерпевают частичную или полную закалку. Холодные трещины возникают в процессе охлаждения после сварки ниже температуры 150°С или в течение последующих нескольких суток. Они могут образовываться во всех зонах сварного соединения и располагаться параллельно или перпендикулярно по отношению к оси шва. Место образования и направление трещин зависят от состава основного металла и металла шва, соотношения компонент сварочных напряжений и некоторых других обстоятельств. В соответствии с геометрическими признаками и характером излома холодные трещины получили определённые названия:
• «откол» – продольные трещины в зоне термического влияния;
• «отрыв» – продольные трещины в зоне сплавления со стороны шва (аустенитного);
• «частокол» – поперечные трещины в зоне термического влияния.
Наиболее часто возникают холодные трещины вида «откол». Образование холодных трещин начинается с появления очага разрушения, как правило, на границах бывших аустенитных зёрен на околошовном участке зоны термического влияния, примыкающих к линии сплавления. Протяжённость очагов трещин составляет несколько диаметров бывших аустенитных зёрен. При этом разрушение не сопровождается заметной пластической деформацией и наблюдается как хрупкое. Это позволяет отнести холодные трещины к межкристаллитному (межзеренному) хрупкому разрушению. Дальнейшее развитие очага в микро- и макротрещину может носить смешанный и внутризерненый характер. [135]
Основными факторами, обуславливающими образование холодных трещин в сварном соединении из легированных сталей, являются:
• структурное состояние металла сварного соединения, характеризуемое наличием составляющих мартенситного и бейнитного типа (Sд, %) и размером бывшего аустенитного зерна (d3, мкм). Свойства указанных структурных составляющих зависят от химического состава и в первую очередь от содержания углерода (C, %);
• концентрация диффузионного водорода в зоне зарождения очага трещины (Hд, см3/100г металла);
• растягивающие сварочные напряжения I рода (σсв, МПа).
Критическое сочетание этих факторов приводит к образованию холодных трещин.
Роль структуры в зарождении очага замедленного разрушения свежезакаленной стали связывают с микропластической деформацией (МПД), в приграничных зонах зёрен. Наличие в структуре такой стали незакрепленных, способных к скольжению дислокаций при действии сравнительно невысоких напряжений обуславливает МПД. Особенно высока плотность дислокаций в свежезакаленном мартенсите. Значения МПД лежат в диапазоне от 10—5 до10—4. Проявляется МПД при напряжениях выше предела неупругости или микроскопического предела текучести σА. Процесс МПД – термически активируемый, т. е. его скорость зависит от температуры и приложенных напряжений. Сопротивляемость замедленному разрушению зависит от времени действия нагрузки и стремится к некоторому минимальному значению σp. min., которое принимают за номинальное значение «замедленной прочности». После отдыха способность закалённой стали к МПД исчезает. Конечные высокие значения твёрдости и предела текучести закалённой стали – результат старения, при котором происходит закрепление дислокаций атомами углерода. Особенности развития МПД достаточно хорошо объясняют приведённые выше закономерности замедленного разрушения.
Механизм межкристаллического разрушения при образовании очагов замедленного разрушения может быть объяснён тем, что максимальные плотность дислокаций и интенсивность МПД приходятся на приграничные зоны зёрен. Это является результатом того, что мартенситное превращение начинается в центральных частях зёрен при температурах, соответствующих верхней части температурного интервала превращения, а заканчивается в приграничных зонах зёрен при температурах, соответствующих нижней части этого интервала. Кроме того, при образовании пластинчатого мартенсита его иглы при выходе на границы зёрен вызывают в зонах, примыкающих к ним, появление высоких плотности дислокаций и уровня микронапряжений. При длительном нагружении по границам зёрен развивается локальная МПД, в результате которой реализуется межзёренное разрушение по схеме Зинера-Стро, предполагающей относительное проскальзывание и поворот зёрен по границам.
Основным источником водорода в сварном соединении является водород в атмосфере дуги, который растворяется в расплавленном металле сварочной ванны. Различают следующие формы существования водорода в металле, в зависимости от его состояния, положения в металле:
• атомарный (или ионизированный) водород – растворённый в кристаллической решётке до предела растворимости (равновесный), растворённый сверх предела растворимости (неравновесный), связанный с дефектами решётки (скопившийся в так называемых субмикроскопических ловушках);
• молекулярный водород – скопившийся в микро- и макропорах, называемых коллекторами.
В зависимости от подвижности в металле различают:
• диффузионный (диффузионно-подвижный) водород Hд – способный к диффузионному перемещению в решётке при появлении градиентов концентраций, температур, напряжений, растворимости (в случае разнородных металлов). К этой форме относится атомарный водород, растворённый в решётке;
• закрепленный водород – не способный к диффузии в металле при данных условиях. К этой форме может быть отнесён атомарный водород в ловушках и молекулярный в коллекторах (его также называют связанным, остаточным, металлургическим).
Все формы водорода находятся в термодинамическом равновесии, зависящем от температуры. При повышении температуры свыше определённого уровня начинается заметный переход одних форм водорода в другие: молекулярного – в атомарный, неравновесного – в равновесный, связанного в ловушках – в растворимый.
Поскольку всегда на поверхности ограниченного тела существует градиент концентрации водорода, происходит непрерывный выход (десорбция) HД в атмосферу. [136]
Через определяенный промежуток времени практически весь водород должен десорбироваться из металла, поскольку происходит переход из одной формы существования водорода к другой. При нормальной температуре относительно быстро десорбируется из металла основная часть диффузионного водорода HД, причём переход закреплённого водорода в диффузионный HД развивается чрезвычайно медленно, т. е. закрепленный водород остаётся в металле практически неограниченное время. Сумма концентраций закреплённого водорода и не успевшего выделиться к данному моменту диффузионного водорода HД составляет концентрацию остаточного водорода H0.
Распределение HД по объёму сварного соединения и его концентрацию в любой заданной точке определяют расчетно-экспериментальным способом. Экспериментальная часть способа состоит в определении исходной концентрации диффузионного водорода в металле шва HШ0, в установлении зависимости коэффициента диффузии водорода DH от температуры для шва, зоны термического влияния и основного металла, а также в определении параметров перехода остаточного (металлургического) водорода H0 в основном металле в Hд и обратно при сварочном нагреве и охлаждении. Расчётная часть способа заключается в решении тепловой задачи (для заданных типа сварного соединения и параметров режима сварки) и диффузионной задачи. Последняя для сварки однородных материалов представляет численное решение дифференциального уравнения второго закона Фика, описывающего неизотермическую диффузию водорода с учётом термодиффузионных потоков в двумерной системе координат.
Основные закономерности насыщения сварных соединений водородом следующие:
1) насыщение различных зон сварного соединения водородом можно охарактеризовать двумя параметрами – значением максимальной концентрации HДmax и временем достижения этой или заданной концентрации tmax;
2) для заданных составов шва и основного металла, толщины металла и типа разделки параметры вида HДmax в основном определяются значениями Hш0, а параметры вида tmax – тепловым режимом сварки.
Действие диффузионного водорода при образовании холодных трещин более всего соответствует одному из механизмов обратимой водородной хрупкости. Его особенность заключается в том, что в условиях медленного нагружения источники водородной хрупкости образуются вследствие диффузионного перераспределения водорода и исчезают через некоторое время после снятия нагрузки. При этом важная роль отводится взаимодействию водорода с дислокациями и облегчённому перемещению их комплексов. В металле сварных соединений Hд концентрируется на границах крупных бывших аустенитных зёрен, которые характеризуются повышенной плотностью дефектов кристаллической решётки.
Влияния водородного охрупчивания на процесс разрушения описывают различными механизмами: адсорбционным (действие водорода как поверхностно-активного элемента), молекулярного давления (в результате перехода атомарного водорода в микропоры и его молизация) и др.
На практике структурное состояние оценивают значением твёрдости. Как правило, в технических условиях на сварку изделий указывают допустимое значение твёрдости в диапазоне 200…350 HV. [134]
1.3.1. Методы снижения образования
холодных трещин в сварных соединениях
низколегированных сталей
Предотвращение холодных трещин в сварных соединениях направлено на уменьшение или устранение негативного воздействия основных факторов, способствующих их образованию. Это достигается за счёт:
• регулирования структуры металла сварных соединений;
• снижения концентрации диффузионного водорода в сварочном шве;
• уменьшения уровня сварочных напряжений.
В зависимости от подхода, методы предотвращения холодных трещин можно разделить на три категории:
• Металлургические методы: Эти методы направлены на регулирование структуры металла сварных соединений путём рационального выбора химического состава основного металла и сварочных материалов. Рекомендуется минимизировать содержание углерода и легирующих элементов, способствующих повышенной прокаливаемости сталей, при этом обеспечивая необходимые механические свойства шва и зоны термического влияния. [132,135,136]
• Технологические методы: Эти методы включают регулирование структуры металла сварных соединений путём выбора оптимального теплового режима сварки. Для этого применяются следующие подходы:
1. Увеличение удельной погонной энергии q/υδ до максимально допустимого значения (при условии качественного формирования шва, соответствующего стандартам);
2. Применение предварительного и сопутствующего подогрева, послесварочного нагрева, а также термической обработки, такой как высокий отпуск или отжиг.